Good day to all!
Report on the construction of a garage in a confined space, tight construction to the borders of neighbors, tight construction deadlines ...
If anyone has questions, I will be glad to answer them!
Thanks for attention.
P.S. I add that the garage built in the end still did not become the garage of my dreams ... all the time there were some half measures. But if once again it happens when to build, then the garage will be 80 squares, two entrances, a kitchen, a TV and a sofa!
Comments 23
As the winter survived the canopy at the entrance and the ramp from the house where the garage. A lot of snow should accumulate there.
Well experienced. The lathing is made with a margin and the thickness of polycarbonate with a margin.
Super! He bookmarked himself - in the future it may come in handy. The approach to business is worthy of respect. It can be seen that the house has a good Boss with the right hands!
Make the same table of contents in your BZ ...
The post is very informative, the garage and awnings are excellent! Everything is done with your own hands, the author has a separate respect for the tile. I wouldn’t dare myself (it’s easier to hire). Good luck operating these buildings, thanks for the post.
Thanks for the kind words!
Considering a wood frame? Not cheaper?
The tree is not my goodness. And if the fire goes out because of the fence? There is nothing in my design that could catch fire in principle. And you can’t sandwich the tree, it will walk, dry out, etc. Only metal. I picked up the panels with the presence of a certificate from firefighters.
If there is a fire, everything will burn, and your frame is metal. just melt.
And if there is a nuclear war, then this does not mean that it is already possible to stop observing the norms of electrical and fire safety today? ))) And if the flood? What about the earthquake? ))) And if tomorrow a brick is on his head, then hell would be with him, with everything ...)))
In any case, it is the fireproof design that significantly increases the chances of survival. And next to the neighbors there are also no capital buildings.
I forgot to mention the meteorite; they have often visited us in Russia recently. Well done, eyes are afraid of hands doing
Very carefully everything turned out! 6+ on a 5-point scale
Thanks. I did my best ))
record has left. how many grandmas came out material. pipes and panels?
About 150 rubles a skeleton (material and work), panels - 150 rubles, panel work - 80 rubles. Small things - another 30 rubles. Gate - 60 rubles, door - 20 rubles, turnkey floor - 50 rubles, electrician - 70 rubles. Sheds - 100 rubles each (material and work).
In short, if you yourself, then they say the price goes
No, the floor, the electrics - my job. You yourself won’t do metalwork with such quality, there’s nothing to save on! In my case, after finishing work on the skeleton, measuring with a laser tape measure showed a difference of 2 mm by 8 meters! The assembler guys themselves were fucked up by the accuracy of execution when I showed them. True, before that I forced them to use their Israeli level for 5 thousand. rubles, which does not know a single drop. Well, he himself helped put up the pillars ... So - the main cost is still for the material, and only 30 percent for work.
Yes, no, you can do everything yourself. I'm not a point. at the beginning of summer, I didn’t even figure out how to lay a brick and a foam block. for 4 months in 2 hands he folded the annex to the house on 24sq.m., he himself made the ceiling, rafter system, closed the roof. everything is shorter. the only windows were already inserted for me by the wizard. because I'm tired of doing everything alone already. and our work is more expensive than 30%. if the price of the block is 130 rubles. PC. then put it 100r. here already all 70% is obtained. main desire, tool and head and everything will work out)
So I did not write that it is impossible! ))) Sure you may. You never know what you can do till you try. But just for your own body it is not very useful, especially when you are not 25 years old. But to work with panels, one person will be needed as assistants. And if we talk about ceiling panels - then another three or four people. They are heavy!
Regarding the cost of work on a block and a brick - you wrote everything correctly, and pay attention to the cost of work from me. The more technological the product, the more it takes on the cost of work on a similar, but less technological material.
I'm 27. I plan on the trail. summer garage build 8 * 6. so far I’m choosing material so that it’s practical and more or less budgetary. the block does not want to put anymore, as it is tired
The disadvantages include:
Short service life - about 45-50 years. Although, according to the manufacturers, the galvanized steel used as the shell of the sandwich panels has high physical and technical properties. Plus, the protection of the shell itself is provided by a primer in combination with an anti-corrosion and polymer coating. Whether it is worth hoping for is up to you.
The inability to install on the walls of dimensional hinged shelves or other heavy furniture designs.
The need to monitor the condition of the castle parts of sandwiches during installation at low temperatures.
The absence of "vandal resistance", as in reinforced concrete structures or brick structures, therefore there is a risk of breaking or surface mechanical damage - chips, scratches.
The use of basalt fiber panels without fail requires good ventilation. Unlike homogeneous materials, mineral wool sandwiches have the worst thermal insulation ability.
The likelihood of drafts due to cracks in the docking areas of adjacent panels in case of violation of the assembly scheme and freezing of the joints of the structure in frosty weather.
A rather high cost of construction, but since buying the same concrete, brick or high-quality lumber is more expensive than sandwiches, then all this is relative.
What is a sandwich panel and why are it so popular in building objects
At its core, the sandwich panel resembles a sandwich sandwich. Where in the middle there is a heater, and on the sides there is a metal frame of different texture. Such blocks are fastened with a hot press; there is no additional need to fasten the elements. A sip or a sandwich panel practically does not leave gaps due to perfectly even edges and a porous structure of a heater. Heat losses when choosing a quality material are minimal.
The outer sheet of the panel is distinguished by a special wavy texture, which gives the structure a finished shape on the one hand, and on the other makes seams and joints less noticeable. In addition, this finish option increases the strength of the walls.
Polymers prevent swelling and decay of the material. It is no secret that high humidity and precipitation adversely affect the natural surface.
Advice! Before buying a material, study its dimensions, check for bending ability, and insulation material for safety. The standard width of the sandwich panel is 1 meter.
Pros and cons of technology: how to deal with them
The main advantage of this technology for the construction of any building is its high speed. And in this case, you do not depend on the time of year. In addition, the purchase of panels will cost significantly less than the usual brick or concrete. In comparison with a conventional metal garage, the panel does not overheat.
- for the construction of a garage from sip panels, you do not always need a foundation,
- the structure is light and strong,
- sheets are quite light and small,
- rich colors and a variety of textures of finishing material,
- the construction is mobile - it can be assembled and disassembled at any time.
For your information! Sip panels have good soundproofing characteristics, then an absolute advantage for the construction of a building in the immediate vicinity of the house.
There are not many shortcomings in sandwich panels. Some of them are:
- if the assembly technology is violated, gaps may form, which may ultimately lead to freezing of the garage walls,
- lack of foundation in viscous soil. Your garage can just "part". So, during sharp gusts of wind or a hurricane, the garage will simply fly away.
What projects are being built
Any construction planning work begins with a blueprint. Naturally, it is worth considering the dimensions of the car.
Usually make technical gaps for the free movement of people around the car. Ideally, if your garage will also mean additional shelves
For your information! According to the standard for a B-class passenger car, you need to build a garage at least 6 meters in length and 4 meters in width.
Most often, the garage door is made standard - swinging out. Recently, rolling shutter systems have been popular.
Very often, such a door is controlled by a remote control. Modern technology allows you to create two-story or two-story garages.
On the upper floors, car owners usually place oversized car care items, such as seasonal tires for wheels
Construction stages
The first stage of any survey work is to understand exactly which garage you want - with the foundation, with what type of door opening, what size.
Typically, the construction technology consists of the following steps:
- Cleaning the area and measuring the boundaries of the future structure.
- Assessment of the need for the foundation.
- Calculation of materials for a metal frame, their purchase and construction of the so-called crate.
- Panel mounting. The technology is not much different from the construction of drywall walls. Bonding goes butt to butt in the grooves.
- Finishing and grouting joints with sealant.
- Inset gate, and, if necessary, windows.
- Wiring electricians.
- Organization of the workspace.
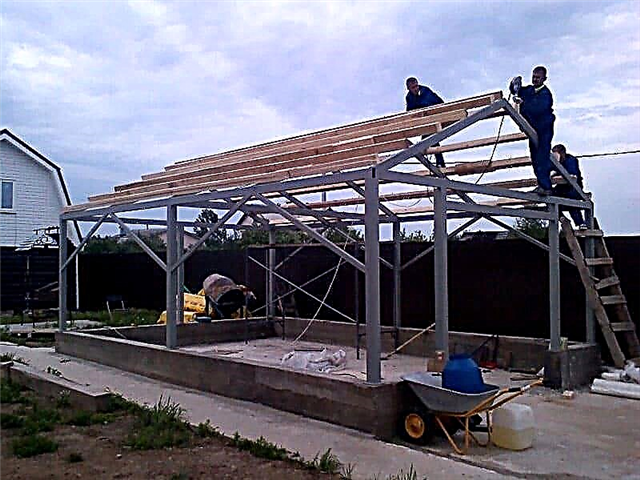
Foundation
As we noted above in the article, such a fairly light type of structure does not require the presence of a foundation. If you are confused by the quality of the soil, you can fill the concrete base.
The most common foundation building methods are tape or columnar.
In the second case, you will need to prepare piles and pillars in advance. This option is extremely rarely used due to its laboriousness. Usually, everything is limited to a strip foundation. If there is no foundation, the trench will still have to be dug, but for the frame fasteners.
Important! The depth of the trench should be at least half a meter. To give greater stability to the base, concrete reinforcement can be laid under the concrete.
At this stage, even before concrete hardens, it is important to remove bumps and bubbles. Otherwise, the concrete base will begin to crumble due to temperature changes. Before installing the frame, it is necessary to lay a layer of waterproofing material, and if desired, insulation.
Frame mounting
The assembly of the frame should not cause any particular difficulties. Sheets of finishing material are superimposed on the vertical and horizontal profiles, to increase stability, the arches are strengthened with welded frames. Wooden beams can be used along the structure.
In some cases, spot welding of joints is acceptable to increase structural strength
Important! Between the foundation and the frame, you need to fix the so-called base crossbar - a layer that not only strengthens the adhesion, but also has hydrophobic properties. After that, we proceed to the installation of the roof frame - the principle is the same, only the profile is one and a half times wider than for walls.
Finishing work
One of the most important stages is the work on sealing joints. If the technology is disrupted, moisture can get into the inner layer, which means the insulation can “swell”, which completely negates all previous stages of work. All installation work starts from the corners of the garage.
The joints are additionally laid with a heat-insulating layer. After drying, sealant is applied.
Conclusions and recommendations
Among other building structures, the sandwich panel stands out for its versatility, accessibility and high aesthetics. However, when working with material, it is worth observing some rules.
Do not rush to remove the protective film into which the sheets are packed. Prior to installation, the panel must be protected from external influences. Panels are very sensitive to point pressure. It can very easily cause chips and cracks.
During installation, try to avoid rough exposure to the material. Even a flat metal ladder can leave marks and damage the integrity of the coating. Control your actions and rely exclusively on the frame during installation.
The equipment with which sheets will be cut and cut should be chosen with great care
It is better not to use the grinder, since during the heating of the disk, it can damage the insulating layer. An ordinary hacksaw or a jigsaw is suitable for sawing small sections, but it is necessary to use the unit at low speeds.
If you are still in doubt whether you should buy a sandwich panel, watch this video.
Table: Pros and Cons of Sandwich Panels
pros | Minuses |
|
|
Despite the many positive qualities, such a structure also looks beautiful
Sandwich Panel Specifications
The sandwich panel is a multilayer plate in which a heater is installed between the outer protective layers. Mineral wool is used as insulation, as well as polystyrene or polyurethane foam boards. The outer layers of the sandwich panels are made of smooth and profiled metal sheets, and the inner ones are made of plastic alloys resistant to chemical attack.
For the construction of a garage, it is better to give preference to panels with a metal coating.
Sandwich panels with a length of 2 to 12 m and a width of 1 m are on sale. The factory width of this building material can be either more or less than 1 m.
The design of the sandwich panels provides a locking part at the edges. It allows you to reliably connect adjacent elements in one plane. Such a connection has good thermal insulation properties, so the walls of the garage will not need additional insulation.
By appointment, the sandwich panels are divided into:
Wall sandwich panels have a smoother surface
Roofing sandwich panels have a ribbed surface
Practitioner feedback on the design
Recently, I had to go on a business trip for several days, and when I returned, I saw a large and beautiful garage at a neighbor in the territory. The idea of building a garage from a sandwich panel now haunted me, and I decided to build. As it turned out, indeed the building was erected as soon as possible (3 days). My garage has dimensions of 4x62, x5 m. The roof of the garage was made gable. A slab foundation with reinforcement was erected. Now it’s cold outside, but the garage maintains a constant temperature. Heat does not escape through the walls. I did not notice cracks and moisture coming into the room.
Nikolay, 02/02/2016
When I first encountered the purchase of sandwich panels, I noticed a big price difference depending on the manufacturers, with relatively the same product quality. The largest price difference was 22%, so you should not rush on the first product that came across. After spending a little time, you can order suitable panels via the Internet.
Sergey Petrovich, 03/23/2016
The question of the immediate construction of a new garage arose when a tree fell from the storm directly onto the roof. As a result, the load-bearing beams cracked and the wall was damaged. In such cases, as a rule, there is not enough money, so I began to think about how to quickly build a quality garage. Friends advised to build a sandwich panel. I reacted with disbelief to this idea, because I did not consider the sandwich panel to be reliable material, and when I saw the construction project I almost abandoned this idea. However, the money was paid, the construction team has already been ordered, and I decided to build. The result exceeded my expectations. The building was erected in a matter of days (4 days), the accuracy and beauty of the building struck me. However, there was still a lack of confidence regarding the thermal insulation properties. For several months now I have been using the garage. Despite the hot times, the inside of the garage is relatively cool.
Anatoly, 07/14/2016
Preparatory phase: drawings, sizes and designs of garages
Preparing for the construction of a garage from sandwich panels involves designing a future building with drawing up drawings and diagrams, selecting a site for construction and selecting materials.
For an average passenger car, the optimal garage size is 6x4 m, with a height of 2.2–2.5 m. These parameters are not any kind of template or established rule.
The size of the construction of the garage should provide for a convenient check-in of the vehicle, as well as free movement of the driver between the car and the wall of the building.
Garage construction of sandwich panels for a passenger car will occupy approximately 35 sq. M.
From the sandwich panels you can build a structure of almost any shape. However, in the construction of garages, projects most often used by time and other owners are used.
The most popular sandwich panel garage designs are few
Material Tips
When buying sandwich panels, you must pay attention to the following characteristics:
- Insulation material. The most common mineral wool, glass wool, as well as expanded polystyrene and polyurethane:
- mineral wool is popular due to its heat-insulating qualities. This material is resistant to open flame, does not emit substances harmful to humans. However, mineral wool is unstable to moisture. Under its influence, it crumbles and loses its properties. It should be borne in mind that walls with mineral wool are not a favorable place for the propagation of fungi, but because of the organic acids secreted by them, wool is destroyed. Mineral wool is obtained by melting metallurgical slag and rocks,
- glass wool in its characteristics resembles mineral wool. However, this insulation has longer fibers, due to which the plates are more durable and elastic. The disadvantage of glass wool is that after a short period of time it is compressed, losing its original thickness by 5-15%. This is especially promoted by the moisture absorbed into the material. Another significant drawback of such a heater is its ability to release small particles of glass into the environment. Getting them in the respiratory tract of a person can lead to serious and sometimes irreversible health problems,
Glass wool is hazardous to health. The smallest particles of glass and dust can appear in your garage over time.
Sandwich paneling can be done from:
- Metal. Typically, such a coating is made of thin sheets of galvanized and stainless steel. In turn, the metal is coated with a polymer layer of plastisol, polyvinyl fluoride, pural or polyester. In addition to these coatings, manufacturers can use aluminum foil, paper or fabric. Panels with such casing are made smooth, knurled, in the form of waves or trapezoidal.
The garage is best built from sandwich panels with metal cladding
Aluminum foil retains heat well and does not leak moisture
As a polymer coating on the surface of the sandwich panel can be used:
- Polyester. Such a layer is marked in the form of capital letters PE. The manufacturer recommended using panels with this coating in all climatic zones for structures located indoors. The polymer coating is sprayed to a thickness of 25 microns, which gives the material stability when exposed to temperatures up to 120 ° C. Sandwich panels with this coating are glossy and matte.
- Plastisol. In the manufacture of this coating, polyvinyl chloride and plasticizers are used. It is marked with capital letters of the English alphabet PVC and a number that indicates the thickness of the layer in micrometers. The advantages of plastisol is its versatility. Sandwich panels with this coating can be used both for indoor and outdoor use. They are highly resistant to mechanical damage, corrosion and metal rolling.
- Polydifluorionad. This coating is labeled PDVF. Polydifluorionade, like polyester, is resistant to temperatures up to 120 ° C, and also does not change its physical and chemical properties when the temperature is lowered to -60 ° C. Panels with this coating are resistant to mechanical damage, aggressive chemicals and corrosion.
- Pural. Such sandwich panels are marked with the English word Pural. The basis for the manufacture of this coating is polyurethane. It has the highest resistance to critical temperatures (from -60 to +120 ° C), chemical attack, corrosion and ultraviolet radiation. Due to the high properties of polyurethane, these panels are most often used for decoration and insulation of external walls of buildings.
Pural-coated sandwich panels - the best option for exterior wall and roof decoration